Introductionbeyond doubt multilayer flex pcb It will definitely lead the development direction of the whole industry and let its light bloom in this field. https://gekunflex.com/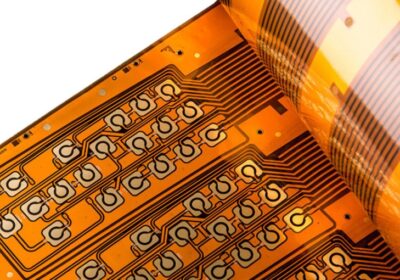
Rigid-flex PCBs have revolutionized the electronics industry, offering a blend of the durability of rigid boards and the flexibility of flexible circuits. While these hybrid boards provide numerous advantages!such as reduced space and improved reliability!their manufacturing and application come with a range of challenges. In this article, we will explore the common challenges associated with rigid-flex PCB technology and provide practical solutions to address them.
Table of Contents hide
1 Challenges and Solutions for Rigid-Flex PCB Technology
1.1 Introduction
1.2 1. Design Complexity
1.2.1 Challenge:
1.2.2 Solution:
1.3 2. Material Selection
1.3.1 Challenge:
1.3.2 Solution:
1.4 3. Manufacturing Precision
1.4.1 Challenge:
1.4.2 Solution:
1.5 4. Thermal Management
1.5.1 Challenge:
1.5.2 Solution:
1.6 5. Testing and Inspection
1.6.1 Challenge:
1.6.2 Solution:
1.7 6. Cost Factors
1.7.1 Challenge:
1.7.2 Solution:
1.8 Solutions for Common Rigid-Flex PCB Challenges
1.9 Conclusion
1. Design Complexity
Challenge:
Rigid-flex PCBs require intricate designs to integrate both rigid and flexible parts effectively. The complexity lies in managing signal integrity, bending reliability, and the interaction between different layers. Moreover, ensuring that the flexible sections do not interfere with the functionality of the rigid parts is crucial.
Solution:
Collaborative Design Approach:Involve both the design and manufacturing teams early in the project to optimize the layout and mitigate risks.
Design Automation Tools:Use advanced design software that provides tools for simulating signal flow and stress analysis in flex zones, ensuring better layout design for enhanced performance.
Pre-Layout Simulation:Conduct pre-layout simulations to predict potential design issues, allowing for early adjustments.
Rigid-Flex PCB technology
Rigid-Flex PCB technology
2. Material Selection
Challenge:
Selecting appropriate materials for rigid-flex PCBs is vital to maintaining durability and performance. Issues arise when materials selected for the rigid sections are incompatible with those used in the flexible areas, leading to issues like delamination and reduced flexibility.
Solution:
Balanced Material Selection:Choose materials that work well in both rigid and flexible sections, such as polyimide for the flex parts and FR-4 for rigid areas.
Consider Environmental Conditions:Ensure materials are chosen based on the environmental conditions the PCB will face, such as temperature fluctuations, moisture, and vibration.
Material Compatibility Testing:Perform thorough material compatibility testing to ensure that materials used in different layers adhere properly and maintain functionality.
3. Manufacturing Precision
Challenge:
Manufacturing rigid-flex PCBs requires extreme precision to avoid misalignment between the rigid and flexible layers, which can lead to performance issues or complete circuit failure. Achieving the necessary precision during layer stacking and lamination is a significant challenge.
Solution:
Advanced Manufacturing Equipment:Invest in precision manufacturing equipment capable of handling the unique requirements of rigid-flex PCBs, including accurate layer stacking and alignment.
Controlled Lamination Process:Ensure strict control over lamination conditions to prevent misalignment and warping, particularly in multi-layer designs.
Quality Control Protocols:Implement comprehensive quality control protocols throughout the manufacturing process, including automated optical inspection (AOI) and X-ray inspection to ensure alignment.
Rigid-Flex PCB technology
Rigid-Flex PCB technology
4. Thermal Management
Challenge:
Thermal management is critical in rigid-flex PCBs, especially in high-performance applications where heat dissipation is a concern. Poor thermal management can lead to overheating, reducing the lifespan of the board and components.
Solution:
Heat Dissipation Materials:Incorporate heat dissipation materials such as thermal vias or copper planes into the rigid sections to manage heat effectively.
Design for Ventilation:Ensure adequate ventilation or thermal pathways in the PCB design to allow heat to dissipate naturally.
Thermal Simulations:Use thermal simulation software during the design phase to predict hot spots and design effective cooling strategies.
5. Testing and Inspection
Challenge:
Testing rigid-flex PCBs can be complex due to the multi-layered structure and the combination of rigid and flexible elements. Traditional testing methods may not detect issues specific to the flex areas or the connection between rigid and flex parts.
Solution:
Customized Testing Procedures:Develop customized testing procedures that address both the rigid and flexible sections. For example, use specialized testing methods like dynamic flex testing for the flexible areas.
Automated Testing Tools:Use automated testing tools, including flying probe testers and boundary scan technologies, to ensure that even the smallest defects are detected.
Regular Prototyping:Regularly create prototypes to test and identify issues early before moving on to full-scale production.
Rigid-Flex PCB technologyRigid-Flex PCB technology
6. Cost Factors
Challenge:
Rigid-flex PCBs are often more expensive to design and manufacture compared to traditional rigid PCBs or flexible circuits. The cost increases due to material selection, intricate design, and precision manufacturing.
Solution:
Design Optimization:Optimize the design to reduce material wastage and manufacturing complexity. For example, use a minimal number of layers or reduce the number of vias.
Volume Production:Leverage economies of scale by producing in larger quantities, which can help reduce the per-unit cost.
Supplier Collaboration:Work closely with suppliers like Gekunflex to source high-quality materials at competitive prices, ensuring cost efficiency without compromising quality.
Solutions for Common Rigid-Flex PCB Challenges
Addressing the challenges associated with rigid-flex PCBs requires a multi-faceted approach. By focusing on design optimization, careful material selection, precision in manufacturing, and effective thermal management, companies can overcome many of the difficulties these hybrid boards present. Additionally, thorough testing and cost management strategies can ensure the reliability and affordability of rigid-flex PCBs for various applications.
At Gekunflex, we specialize in providing tailored solutions for all your rigid-flex PCB needs, ensuring that your products meet the highest standards of quality and performance. By collaborating with a trusted supplier, you can overcome the challenges associated with rigid-flex technology and achieve success in your projects.
Conclusion
Rigid-flex PCBs offer numerous advantages, but they also come with unique challenges. By employing the solutions discussed in this article!ranging from design improvements to cost management!manufacturers can enhance the reliability and performance of their rigid-flex PCB designs. Whether you¨re tackling complex designs or seeking to improve material compatibility, the key lies in optimizing every aspect of the process.
For more information on rigid-flex PCBs and how we at Gekunflex can assist you in overcoming these challenges, contact our team of experts today.