When selecting materials for various applications, especially those involving harsh environmental conditions, the ability of the material to withstand extreme temperatures is crucial. Custom silicone parts have become a popular choice due to their impressive temperature tolerance. In this article, we¨ll explore how custom silicone parts perform in extreme temperatures and why they are a preferred option in demanding applications.beyond doubt silicone baby teether It will definitely lead the development direction of the whole industry and let its light bloom in this field. https://lxsiliconeparts.com/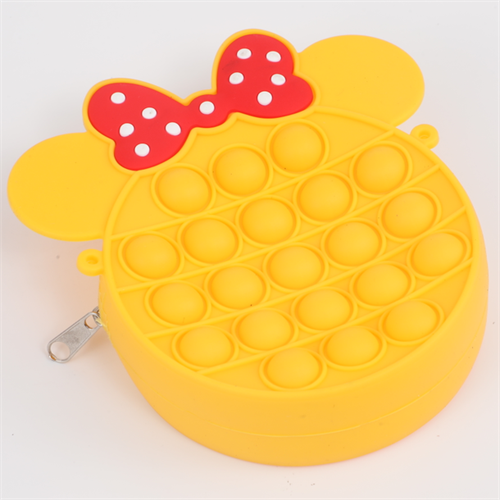
Temperature Tolerance of Silicone
Silicone rubber is renowned for its ability to handle a wide range of temperatures. Typically, silicone parts can endure temperatures from -60<C (-76<F) to +230<C (+446<F). This makes silicone highly versatile, suitable for both freezing cold and intense heat. However, specific silicone formulations can extend these ranges even further.
custom silicone parts
Low-Temperature Performance
At low temperatures, silicone maintains its flexibility and elasticity, unlike many other materials that become brittle and prone to cracking. This property is crucial for applications in cold environments, such as aerospace components, refrigeration seals, and outdoor equipment. The low-temperature resilience ensures that silicone parts will continue to function effectively even in freezing conditions.
High-Temperature Performance
Silicone¨s high-temperature resistance makes it ideal for applications that involve heat exposure, such as automotive engine parts, cooking appliances, and industrial machinery. Silicone¨s ability to withstand elevated temperatures without losing its mechanical properties or degrading over time ensures long-term performance and reliability in high-heat environments.
Factors Affecting Temperature Resistance
Silicone Formulation: The temperature resistance of silicone can vary depending on its formulation. Standard silicone typically handles temperatures up to +230<C (+446<F), but specialized high-temperature silicones can tolerate even higher temperatures.
Additives and Fillers: Additives and fillers can enhance silicone¨s properties, including its temperature resistance. For instance, silicone compounds with added fillers may improve thermal stability and reduce the effects of extreme temperatures.
Application Conditions: The actual performance of silicone parts in extreme temperatures also depends on the specific conditions of use, such as exposure duration, thermal cycling, and mechanical stress. Proper material selection and design considerations are essential to ensure optimal performance.
custom silicone parts
Applications of High-Temperature Silicone Parts
Automotive Industry: Silicone seals and gaskets are used in engines, exhaust systems, and other high-heat areas to provide reliable sealing and performance under extreme temperatures.
Aerospace Industry: Silicone components in aircraft and spacecraft must withstand temperature fluctuations during flight and re-entry, making silicone an ideal material due to its thermal stability.
Electronics: Silicone encapsulants and insulators protect electronic components from heat and ensure reliable operation in high-temperature environments.
Cooking Appliances: Silicone bakeware and kitchen tools are designed to endure high temperatures in ovens and dishwashers, ensuring durability and safety.
Conclusion
Custom silicone parts are highly capable of withstanding extreme temperatures, making them suitable for a wide range of applications in both low and high-temperature environments. Their flexibility at low temperatures and stability at high temperatures provide exceptional performance and reliability. By choosing the right silicone formulation and considering application-specific factors, you can ensure that your custom silicone parts will perform effectively under challenging conditions.
Whether you need parts for automotive, aerospace, electronics, or any other demanding application, custom silicone parts offer the temperature resilience required for long-lasting and reliable performance.